BEKLÆDNING AF DØRKARM
Sakst fra den Engelske Morganklubs medlemsblad Miscellany
Technical Miscellany
March 2001 - 26
Trimming door sills
Whilst restoring my Morgan over the past 5 years or so I have read a number of articles about ‘soggy sills’ and now to avoid them. The final solution for me was a combination of much of what I had read so I can’t claim any credit for originality.
I started by building up of few layers of thin ply, shaped to fit around the fuel pipe and wiring loom (that sit on top of the sill) until I had a platform bridging across the full width of the sill (see sketch). These layers of plywood were glued together (but not to the sill) and the bottom layer had a few large holes cut in it to accommodate the heads of the various bolts that held the sill to the chassis.
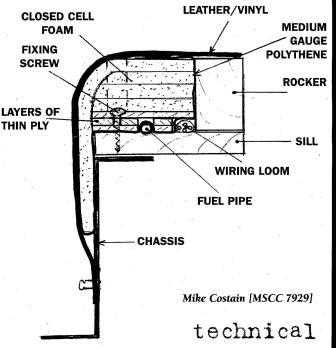
Having achieved a level platform of plywood I then continued with layers of closed-cell foam. I used a sleeping mat, the sort that campers use, as they are designed specifically not to absorb moisture. One mat was more than enough for both sides and cost a mere £4 from Blacks.
After much experimenting with various glues I found that the best thing to stick the layers of foam together was double sided sticky tape that carpet fitters use. I built up the layers of foam until they rose above the top of the rocker then I cut the whole lot level with the top of the rocker using a coarse hacksaw blade. Also using the hacksaw blade I gave a bit of shape to the inner edge to make a smooth curve along the frill length.
The next stage was to remove the bottom-most layer of foam and throw it away! By doing this, the top-most layer was exactly one foam thickness below the top of the rocker. Next I took a larger piece of foam and stuck it on top wrapping it down the side of the assembly so that it reached at least halfway down the depth of the chassis. This gave a nice smooth edge to the now padded sill.
Then I drilled through the foam with a half inch tank cutter down as far as the plywood in a couple of strategic positions followed by a much smaller hole through the plywood so I could screw the assembly to the wooden sill.
Before screwing the assembly to the sill I took a sheet of medium gauge polythene (about 4ft long and 2ft wide) and laid it over the frill length of the sill. Then I placed the ply and foam assembly on top of the polythene and screwed it into position. Once the assembly was in position with polythene trapped under it I wrapped the polythene over the assembly from the top and the bottom and tucked in the ends to encase the whole thing. Then I used copious quantities of ‘duck’ tape to hold it in position and keep it all smooth. Finally I covered the whole lot in black leather using tacks at the top in the conventional but with clips at the base so that I could open it up from the bottom if I wanted to inspect the sill at any time.
I can’t profess that this is the perfect solution because it is still very early days. However it looks good, feels solid but with a bit of ‘sponginess’ and I am reasonably confident it won’t absorb water. My thanks go to all those Miscellany contributors over the past 5 years whose ideas I shamelessly plagiarized!
Mike Costain (MSCC 7929)